GINPLATE NI 4320 AutoP is a Midphos, self-pH-regulated electroless nickel-plating (ENP) process, which provides a mirror bright finish. Midphos ENP is commonly used on components exposed to mild environment for
Continue reading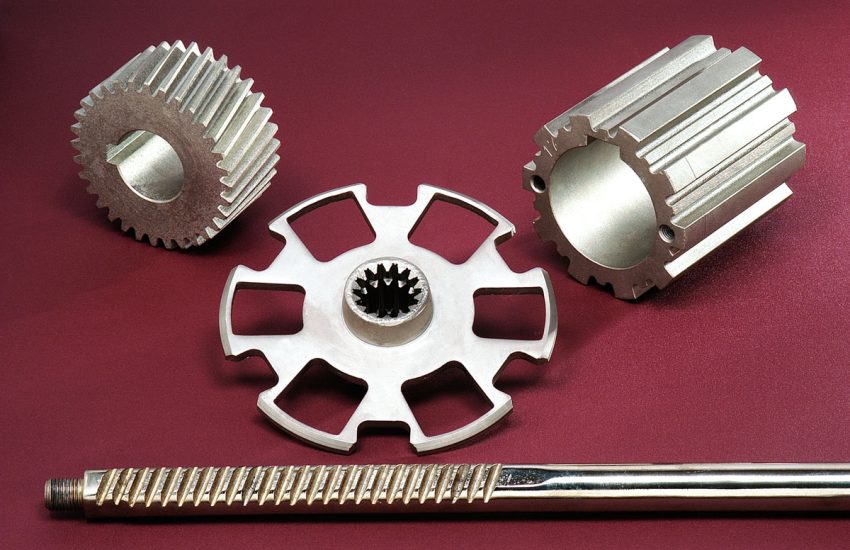
GINPLATE NI 4320 AutoP is a Midphos, self-pH-regulated electroless nickel-plating (ENP) process, which provides a mirror bright finish. Midphos ENP is commonly used on components exposed to mild environment for
Continue readingElectroless Nickel Plating (ENP) is the deposit of a nickel-phosphorous alloy coating by autocatalytic chemical reduction – without the electric current. The majority of ENP for engineering purposes is a
Continue readingCall Us Now
Phone: +91 22 66993000
Send a Message
Support: corporatecommunications@growel.com
Main Office
Growel Corporate, Akurli Road, Kandivli (E),
Mumbai - 400 101, Maharashtra, India
Grauer & Weil (India) Limited © 2022.