At Growel, automation is at the heart of all our plating plants. Keeping this in mind our team, in technical collaboration with Utikal Automation Germany, is working with GalvCon V4.0, a PC-based software exclusively developed for atomization of surface finishing processes. The software is developed to be rich in features and provide ease in operation even when there is a need for replacement and modification.
This automation package is developed in such a way that the “intelligent part” of the software is written on the PC whereas the “driving program”, which rarely requires any changes, is written to the PLC. A highly reliable and powerful TCP/IP connection is established with Siemens S7 controller which requires no special drivers or third-party software for communication.
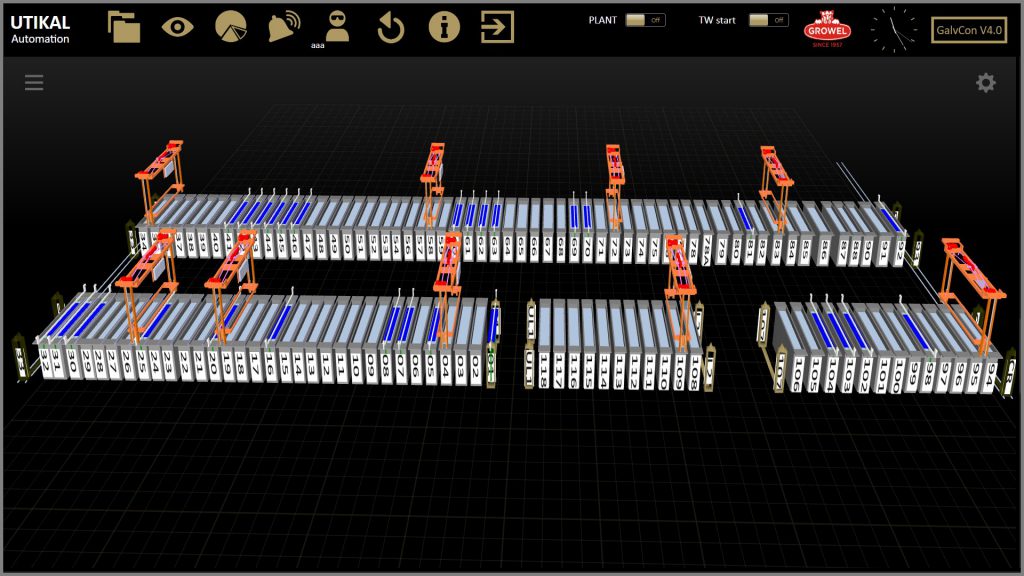
Initiating the plant operation is as easy as entering the article number and quantity to be loaded, the software initiates the cycle with minimum manual intervention.
Each article is pre-assigned with a unique process flow program (sequence of movement with time) and a power program (current density setting). Every article is capable of having a different process flow and current density program. The system has no limitation on the number of articles and their subsequent programs. The process program is designed to include parameters such as order of the baths, residence times, current setting in electrolytic baths, automatic dosing, temperature control in heating/cooling baths, and control of accessories along with visualization. The most powerful feature of this software is the capability of having flexible cycles. With this feature different articles having different process flow programs (different articles need to be processed in different baths with different timings) can be loaded onto the plant as per the user’s output demand.
The software is designed in such a way that the operator is allowed to load articles randomly as required and the intelligence of the software will decide the right sequence of the flight bar movement in the plant. The loaded flight bars may be temporarily stored at the buffer station or maybe directly taken for processing. The software will calculate the most efficient sequence of flight bar entry into the plant ensuring the most optimal usage of the baths and the transport wagons.
GalvCon V4.0 enjoys the following features and advantages:
- Multi-level Password protection for avoiding operator level errors.
- Multiple computers can be connected in the network for visualization but only one PC has the master process control.
- Remote system connectivity is possible for process and status visualization through the Internet.
- A special Loading terminal can be provided, to select the article while loading with visual identification.
- Vast flexibility for process control.
- Software can be quickly tailored to suit user needs.
- Process and current programs can easily adapt to change in plant structure.
- High stability and reliability.