Automobiles, by design, feature metallic parts which are prone to the elements of dust, water and temperature. Corrosion resistance then becomes indispensable. In such a scenario, OEMs must use chemically
Continue reading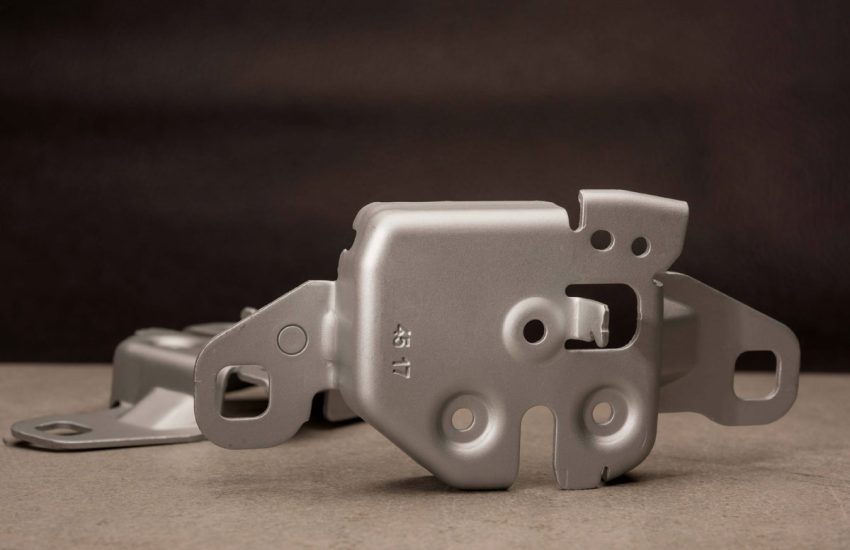
Automobiles, by design, feature metallic parts which are prone to the elements of dust, water and temperature. Corrosion resistance then becomes indispensable. In such a scenario, OEMs must use chemically
Continue readingThe garment industry constantly evolves, with new fashion trends emerging regularly. A versatile tool, zippers are employed in haute couture, business to casual wear, as well as footwear and bags.
Continue readingDifferent advantages of zinc aluminum flake coating are as follows : No Hydrogen embrittlement – The treatment process of zinc aluminum flake coating do not involve treatment with acid for
Continue readingGINPLATE NI 4320 AutoP is a Midphos, self-pH-regulated electroless nickel-plating (ENP) process, which provides a mirror bright finish. Midphos ENP is commonly used on components exposed to mild environment for
Continue readingUse of ferrous and non- ferrous material is unavoidable in the industry due to its availability, strength, durability, work-ability and ability to recycle. Automobiles, bridges, house- hold appliances, power generation
Continue readingThe demand for the chemical industry in India is ever increasing. Chemicals have become a necessity as they have vast and varied uses. They can have adverse effects on
Continue readingThe chemical industry has been considered as a foundational element of the global economy for the whole modern era. This has been a current scenario. It has been founded that
Continue readingThe chemical industry has always been a foundational element of the economy globally for the entire modern era. The chemical industry is the one on which more than 96% of
Continue readingSince a decade, the chemical manufacturers in India have progressed from non-differentiated simple manufacturing of chemicals to an advanced version of the manufacturer of R&D concentrated chemicals. The Indian chemical
Continue readingElectroplating chemicals manufacturers have a huge role in the growth of the latest technology and processes used in the manufacturing field. If a person wants to buy electroplating chemicals, one
Continue readingCall Us Now
Phone: +91 22 66993000
Send a Message
Support: corporatecommunications@growel.com
Main Office
Growel Corporate, Akurli Road, Kandivli (E),
Mumbai - 400 101, Maharashtra, India
Grauer & Weil (India) Limited © 2022.