The Indian lubricant industry has recently opened up new markets. The strong growth in India’s energy, engineering, and automotive sectors is a boon for lubricant manufacturers. In the automotive sector, as consumers migrate to efficient vehicles and motorcycles, they
Continue reading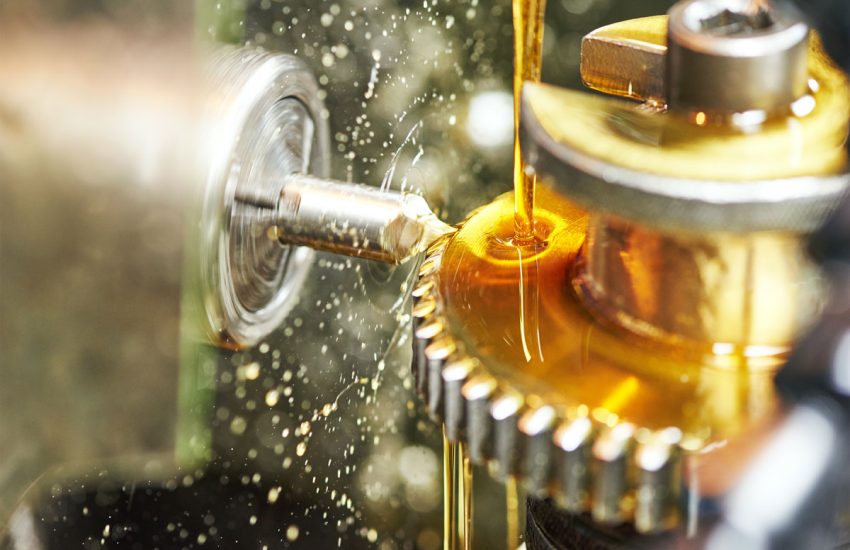