Automobiles, by design, feature metallic parts which are prone to the elements of dust, water and temperature. Corrosion resistance then becomes indispensable. In such a scenario, OEMs must use chemically
Continue reading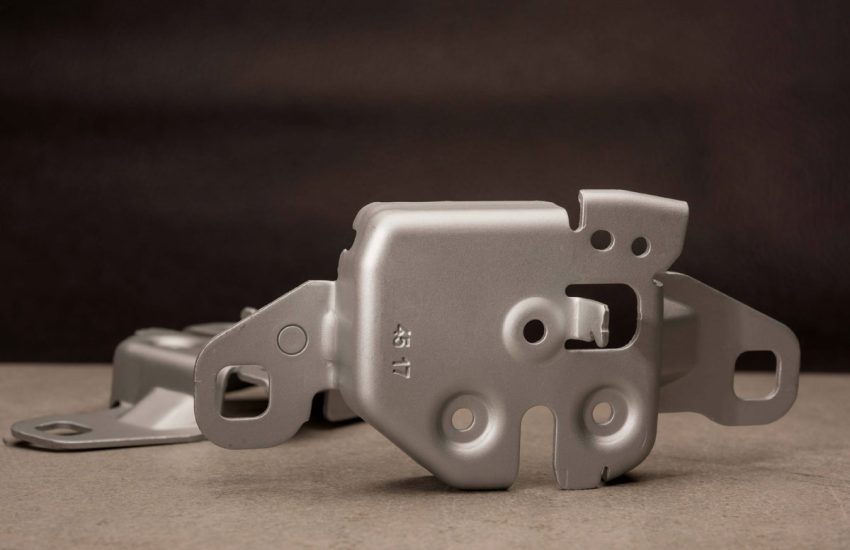
Automobiles, by design, feature metallic parts which are prone to the elements of dust, water and temperature. Corrosion resistance then becomes indispensable. In such a scenario, OEMs must use chemically
Continue readingThe history of the zipper is fascinating. It is the sole reason why Levi’s blue jeans came into existence. It holds everything together, from leather jackets to boots, from winter wear to
Continue readingThe garment industry constantly evolves, with new fashion trends emerging regularly. A versatile tool, zippers are employed in haute couture, business to casual wear, as well as footwear and bags.
Continue readingDifferent advantages of zinc aluminum flake coating are as follows : No Hydrogen embrittlement – The treatment process of zinc aluminum flake coating do not involve treatment with acid for
Continue readingUse of ferrous and non- ferrous material is unavoidable in the industry due to its availability, strength, durability, work-ability and ability to recycle. Automobiles, bridges, house- hold appliances, power generation
Continue readingElectroless Nickel Plating (ENP) is the deposit of a nickel-phosphorous alloy coating by autocatalytic chemical reduction – without the electric current. The majority of ENP for engineering purposes is a
Continue readingGrowel Specializes in the development & manufacture of lubricating oils used in the wire drawing industry. The Indian Market hitherto was dominated by multinational corporations, Growel drawing oil has developed
Continue readingGrodal Syncool 2 is the “GROWEL” make surface protector cum coolant widely used in Pump Industry for Submersible / Open well / Self Priming Pump-sets. Its primary application is to
Continue readingAt Growel, automation is at the heart of all our plating plants. Keeping this in mind our team, in technical collaboration with Utikal Automation Germany, is working with GalvCon V4.0,
Continue readingIn the early days of glass processing, water was used as a coolant and lubricant. However, the use of diamond-tipped tools in glass processing with only water as a coolant
Continue readingCall Us Now
Phone: +91 22 66993000
Send a Message
Support: corporatecommunications@growel.com
Main Office
Growel Corporate, Akurli Road, Kandivli (E),
Mumbai - 400 101, Maharashtra, India
Grauer & Weil (India) Limited © 2022.